A research group from TJU, led by Professor Zhao Naiqin, together with Professor J. Tour’s group from Rice University, has successfully developed the laser-induced three-dimensional (3D) printing method for in situ synthesis of graphene foam (GF) by combining the metal powder 3D printing method with the previous study of powder metallurgy template method for 3D GF synthesis (ACS Nano, 2016,10,1411), as shown in figure 1. This project was jointly funded by the National Natural Science Foundation of China (NSFC), the China Scholarship Council (CSC), the Special Foundation for Science and Technology Major Program of Tianjin and the AFOSR MURI project.
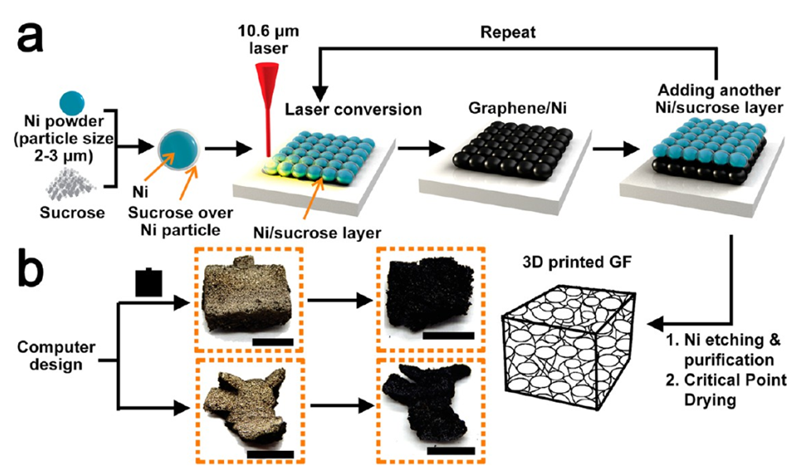
Figure 1 (a) Schematic of 3D printed GF synthesis process. (b) Photographs of 3D printed GF before and after Ni etching. (The scale bars are 5 mm.)
Several methods have been developed to prepare 3D GF, such as chemical vapor deposition (CVD) using Ni or Cu foams as the carrier and catalyst, the template method using NaCl and hydrothermal self-assembling method. However, the above methods still have limitations such as inability to control pore structures, incapability to be free-standing, and low mechanical strength. That said, strong acid, strong oxidant and other non-environment-friendly raw materials are required in the method preparing graphene oxide (GO). The 3D GFs prepared by using GO has many deficiencies including low degree of crystallization. The cold-press molds and a 2.8h heating and cooling process were also needed in the previous research of the powder metallurgy template method. Thus, it is important to develop a simple and efficient method to prepare 3D carbon nanomaterials directly.
3D printing is a simple and efficient technique enabling the preparation of bulk objects, which has received much attention in recent years. In the research of 3D carbon materials, the precursors are limited to the inkjet-printable or UV-curable inks, while the precursors of GF are mostly GO or chemically modified graphene. In this research, the traditional powder metallurgy method is combined with the metal powder 3D printing technology to make the 3D GF growing process by in situ 3D printing method a reality. The process is simple and efficient, with no high-temperature CVD furnace employed and no extended growth process applied.
In this research, the effects of the laser duty cycle and the rastering speed on the GF’s growth and shaping have been studied. In general, a higher laser duty cycle and a lower rastering speed are more conducive to the growth of GF. Under the laser, the sintered Ni scaffolds serve as the template and catalyst of the 3D printed GF, which retain the shape of Ni scaffolds when the scaffolds are moved. As shown in figure 2, the 3D printed GF feature a porous and multilayered structure, consisting of two dimensional (2D) graphene nanoparticles and carbon spheres. The 3D printed GF have a large porosity of 99.3% and a low density of 0.015 g cm?3.
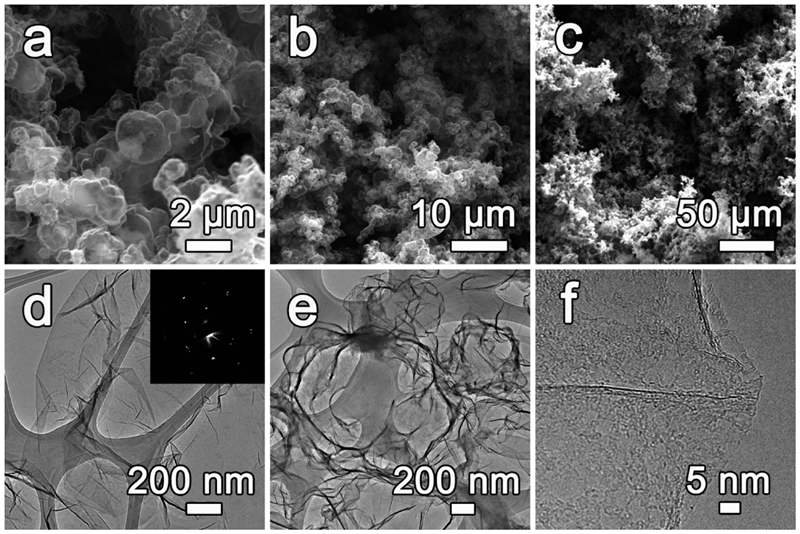
Figure 2 SEM images (a-c) and TEM images (d-f) of 3D printed GF.
It is found that 3D printed GF have similar properties compared with GF grown by CVD, such as comparable electrical conductivity (~8.7 S/cm), energy storage modulus (~11 kPa) as well as a higher damping capacity (Tan Delta: ~0.06). This simple yet efficient method requires neither cold-press molds nor high-temperature CVD treatment. In addition, various 3D carbon materials could be produced by changing the precursor’s composition. The 3D printed GF will be extensively applied to energy storage devices, catalyst, damping materials and many other fields.
The research results have been published in the ACS Nano (DOI: 10.1021% acsnano.7b01987). Sha Junwei, a doctoral student in the research group, and Li Yilun, a PhD student in Professor J. Tour’s research group, are co-authors of the article. Mr. Robert H. Smith of Qualified Rapid Products, Professor Pulickel M. Ajayan’s research group at Rice University and Professor Jun Lou’s group also give strong support to the project. Once published, the results were reported by Rice News and reprinted by more than 20 media outlets such as the EurekAlert (AAAS news portal):
Official Website of Rice University:
http://news.rice.edu/2017/06/21/rice-u-chemists-create-3-d-printed-graphene-foam/
EurekAlert(AAAS)
https://www.eurekalert.org/pub_releases/2017-06/ru-ruc062117.php
Translated by Gong Yiwei
Editors: Yin Wei & Doris Harrington